There has been some progress on the C.B. It is strong but heavyer than I like. Last boat became to heavy. But to cite Churchill when his wife nagged him about spending to much money. We must save she said. No Churchill said we must make more money.
On this line I have given this present boat a lot of displacement. The big modell, the 1/8 was test sailed with 1850 kilos scaled up displacement.
All structures brake down. It is only a question of time. If I will not have the means of leaving from the southern hemispere I will leave from Kinsale Ireland like last time. That means I have to be at sea for maybee 18 months. In that long time in rough weather a lot of wear will occour. Therefore I now give her scantlings to match. The C.B. weighs in at 15 kilos.
To enlarge click once or twice.
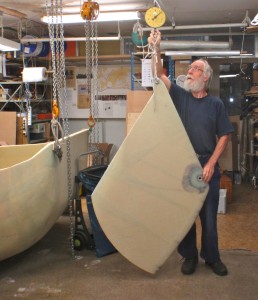
Here is the start of the C.B-case.
Here a picture of he pattern.
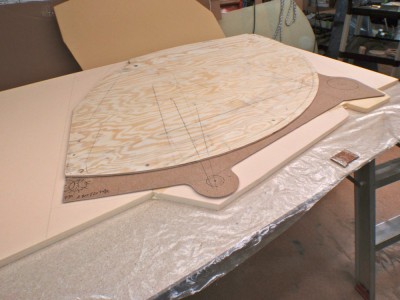
As can be seen I have to glue on additional pieces of Divinycell H130. To clamp them I use wedges.
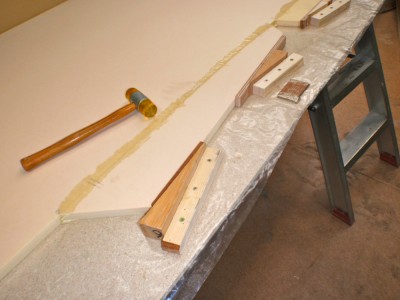
It is handy to be able to cut out the shape on the table. To be able to do that I have shortend the jiggsaw blade to the thickness of the Divinycell 2cm.
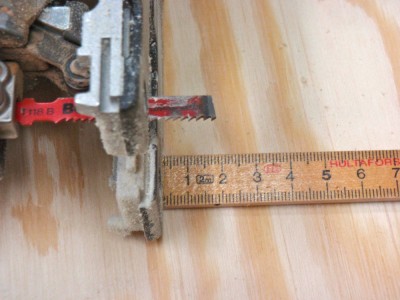
Here cutting. The saw blade cut through the Divinycell but not the table.
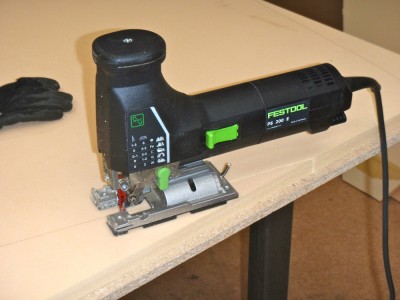
I thank Petter for helping me to laminate.
To be continued…
Regards Yrvind.
Like this:
Like Loading...