CROWDFUNDING WITHOUT MIDDLEMEN
YOU WHO WOULD SUPPORT MY PROJECT MAY SWISH THE CONTRIBUTION TO +46 706 200 550 OR USE THE DONATION BUTTON
SVENYRVINDEXLEX IS MY YOUTUBE CHANNEL A VIDEO EVERY DAY
HI nowadays I mostly do videos on You Tube.
Link below
https://www.youtube.com/@SvenYrvindExlex
Search for Yrvind will most often get you there.
So far there have been one every day since I started to build Exlex in August 2021.
I suggest you become a subscriber as progress on Exlex is well shown by the videos
Regards Yrvind.
ONE YEAR SUMMARY
ONE YEAR SUMMARY.
I started this boat 6.27 X 1.4 meter 21 of August 2021.
The intended use was a sail to Dunedin NZ.
Plans have changed one reason is that Australia told me that I could not stop in Albany south west Australia to reprovision unless I phoned Canberra. The reason for the phone call was that they said that there was no email in Canberra. I do not like when people are dishonest with me.
An other and more important reason is Putins war.
The plan is now for Valdivia in southern Chile.
Valdivia hopefully will provide me with food less processed than what I eat here.
via stopping in Azores, Falkland Islands.
The change of destination and route have made me make a major change the design.
I have decided to have twin keels instead of moving ballast.
I have also changed the bulkhead hatches from solid ones to canvas.
I found that the bow centerboard took to much place and eliminated it, then I changed my mind again and made one slightly smaller.
I planned a stern hawsepipe for a drogue but changed that for a drum winch that can be taken below when not in use.
Sail area have increased from 4 square meter on the previous boat to 12 square meter on three free standing mast two of them side by side.
One important reason for the side by side mast is that the holders will be out of the way of the accommodation. An other reason is that when sailing down wind the boat will be very course stable as was the 2018 Exlex that had a similar rig.
AN INTRODUCTORY VIDEO TO MY SAILING LIFE WITH SAM HOLMES.
Sam Holmes have been here end of July 2022.
He have been helping me to do an introductory video to my boats and sailing. It started 1962 in August when I for the first time left Sweden as Captain of my own boat a 15 feet open boat that I had converted.
Enjoy.
If you’re interested in contributing links are below.
https://www.paypal.com/donate?hosted_button_id=2MYSYADM4594Q
Swift 0706200550
For more videos see my youtube channel.
For some time there have been a new video every day.
Regards Yrvind.
A few words about why I chose the balanced lug sail.
Rigs junk, Ljungström balansed lug.
Wave Rover suggested the junk rig.
I have considered the junk rig.
In my case what speaks against it is that I am not familiar with it.
Also the junk sail is tied to the mast, I prefer the balanced lug that is only attached to the mast by the halyard. That makes it is easy to lower the yard, boom and sail and put the bundle on deck. In strong winds that reduces the wind resistance.
Also the junk sail is sheeted from a point aft the sail. That makes it difficult to find a point for the sheet on deck.
The balanced lug do not have that problem. It can be sheeted from a point below the boom.
Then there is the battens. I worry that they may break. True I can have many spare ones, still it is a disadvantage that have to be considered.
The Ljungström rig is good on the wind, but triangular sails have the worst planform. With vertical battens it can be solved but it complicates it.
Downwind it is complicated to put out a whisker poole and its boom vang.
The small balanced lug can be easily reefed. Ordinary it will only take one or two minutes therefore there is no reason for me to change to junk rig because ease of reefing. The area of each of my sails is only 2.7 square meter and I do not think I will reef often as it is very easy just to drop one or two of the three sails.
A rough provisional estimation of the itinerary for my Cape Horn doubling.
Doubling the Horn
Provisional itinerary
Doubling the Horn entails sailing nonstop from a point above the 50th parallel in the Atlantic, down around the Horn and back to a point above the 50th parallel in the Pacific. Only this near 1,000-mile passage is considered a genuine Cape Horn rounding.
According to legendary author and seaman, Alan Villiers, “nothing else counted as a rounding, for the eastward passage before westerly gales was reckoned no rounding at all.”
Why do I have this desire to doubling the Horn?
Nothing could be more difficult for a small boat and so far no solo sailor have done it in a small boat.
For me the easy life is not satisfying.
Also the European recreational boating directive have outlawed sales of small ocean going boats arguing that they are not safe. I do not deny that it would please me to prove them wrong, but the voyage for me is mostly about the lore of the Horn.
Here is some of the distances and my estimated speed.
Departure from Ålesund Norway will be more or less beginning of June. The distance to Horta Azores is 2100 miles.
The estimated duration of the passage is 60 days.
Average speed, 1,5 knots.
Departure from Horta Azores will be more or less beginning of September. The distance to Stanley Falkland is 6500 miles
The estimated duration of the passage is 90 days.
Average speed, 3 knots.
Departure from Port Stanley, Falkland Islands will be more or less beginning of January to a point north at latitude 50° south then turning south towards Cap Horn then towards Isla Chiloe Chile. That distance is about 2300 miles.
The estimated duration of the passage is 80 days.
Average speed, 1.2 knots.
Being a solo sailor I do my best to avoid areas with much shipping. My previous plan was too provision in Uruguay. Unfortunately there is a lot of trafic coming out of the la Plata river from Buenos Aires and Montevideo.
I dit not consider the Falkland Island as a place to provision as their position is more south than latitude 50° south.
Then I got the idea that when leaving Stanley I will sail north passing 50° latitude south.
This is vanity, still the lore is tempting me.
1980 I cruised the Falkland Islands for four months in my 19 feet boat. The winds was often strong on three different occasions it blew more than 100 knots.
Had my boat had less draft much had been gained. I decided that my next boat would be a shallow draft boat that could take the ground.
With the help of John Letcher in Maine I designed a twin keeled double ender.
I started to build her in the early 1980-s eventually but she was replaced by the the bow centerboarder Bris Amphibie.
Now I combine bow centerboard and bilge keels. Each of these two elements fills its own unique purpose.
It would be interesting to return to the Falklands and see how my ideas works out.
When will I start? Not this year 2022 , not next year 2023, the year 2024 is possible but unlikely as I like to conduct sea trials both inshore and offshore before setting off. Maybee the year 2025 will be my year of departure.
Fate do interfere with even the best laid plans. We just had the Corona pandemic now we have Putins war and who knows what that will lead to.
Please support my project by donations
To be continued…
Regards Yrvind.
16 BETTERMENTS
16 BETTERMENTS ON EXLEX THE SAILING CANOE.
1. Being a double ender her shape is more suited to her average speed length ratio or Froude number than previous boat.
2. Her side by side Ljungström rig makes for much more easy reefing. It also betters her windward performance.
3. Her pivoting center board can be lowered and rise with ropes from the aft deck hatch. That makes control more easy.
4. Exlex 2020 had lee helm I hope to be able to get either lee or weather helm with better position of masts and lateral area.
5. Exlex 2018 and 2020 had problems with steering from the bed room. The solution now to let the rudder axis coming up through the hull.
6. Exlex the sailing canoe have air locks in her bow and stern compartment so that when I work from the deck hatches no water can enter the living area.
7. Exlex the sailing canoe have a 70 mm thick Divinycell core compared to 40 mm in previous boats. This gives better insulation. Her deck hatches do not have have cold spots like her predecessors.
8. Exlex the sailing canoe have 84 kilos of mowing lead ballast. This will greatly increase her stability.
9. The new route via Cape Horn to the Pacific Ocean is more difficult but the estimated passage time is 100 days instead of 180 days because the route is much shorter. This means that the boats displacement at the start of the passage will be much lighter and that I will not lose so much muscles.
10. The bed of the new boat is 10 cm wider. That is an increase, from 70 to 80 cm.
11. She have more volume for stowage and it is better arranged.
12. She will have better visibility from inside the living area, the dining room and bed. It will be 360°.
13. She will have a rudder indicator so that the rudders position can be known without leaving the bed.
14. Her steering will be changed from tiller to quadrant with Dynema lines leading to one steering wheel in the area and on other steering wheel in the bed room. The steering wheels can be locked in position. They will also be able to function as rudder indicators.
15. Betterment is also deck space that I can make walks on even if short ones.
16. The sail area is increased from 4 square meter to 7 square meters. Two sails of 3.5 square meter each, same area as two Optimists dinghy.
This list may not be complete and it is likely that I come up with more betterments.
Stay tuned and please support my project with donations.
To be continued…
Regards Yrvind.
EXLEX THE IDEA
THE IDEA
My idea is to create a good cruiser. I like her to be small, simple, have shallow draft, be trailerable, be propelled by sail and oar.
For me this is an interesting design and building problem.
An interesting test would be to trail her to Ireland or Norway then sailing south and doubling Cape Horn.
For many the ideal cruiser is a well equipped fifty footer. The prise for such a boat ready to sail is abot a million dollar and the yearly running cost about 10 % of that.
The present boat Exlex is a canoe yawl with a bow pivoting centerboard. She will have 84 kilos of lead as mowing ballast.
She is 6.27 cm long, have a beam of 1.4 meter, with a draft of about 0.4 – 0.5 meter.
She will have two freestanding, rotating, side by side, masts with a length of about 3.5 above deck. Each of those mast will carry 3.5 square meter sail area. In addition 0.5 meter from the stern is the mizzen mast she will have 1 square meter sail. In all she will carry 8 square meter sail area, twice as much as the previous Exlex.
Her displacement with food and water for 100 days is estimated to be about 1 metric ton.
I believe my idea is more realistic as she will give more satisfaction, give less worry. One more good thing is that she will use far less of our non renewable resources.
Below two pictures of the 1:20 modell.
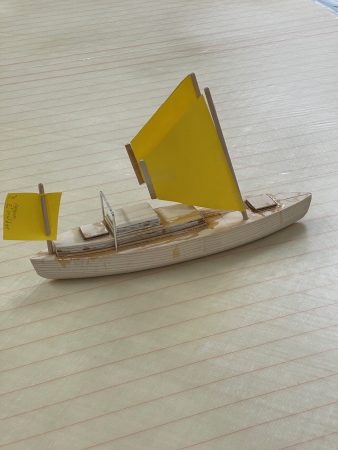
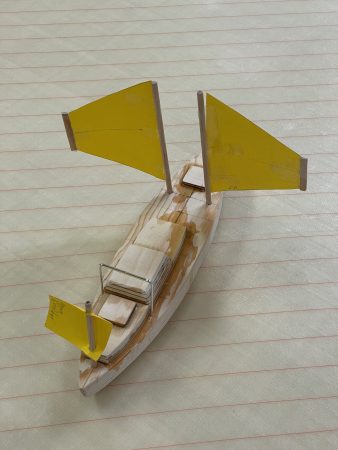
Please support my project by donations via Pay pal or Swish 0706 200 550
To be continued…
Regards Yrvind.
A NEW YEAR A NEW IDEA A NEW ROUTE
A new year a new idea and a new route.
Often small small details have big consequences. Doing the mock up for the dining room I had put, below the seat twelve five liter plastic water cans as part of the water storage. My plan was to do a long sail to New Zealand. Madeira to Dunedin is about 14 000 miles. With an average estimated speed of 75 miles per day it would be about half a year.
There where refilling places on the route, but none really appealing.
To stop in Uruguay would add miles.
In South Africa, there was a lot of traffic it was stormy, there was also much crime I heard.
Australia demanded a visa. I had written to their embassy in Stockholm. You have to call Canberra came response and they have no e-mail. Sure they must have e-mail in Canberra. I realized that they tried to make it difficult for me and got angry.
With just nine cans I would have a bit more space I thought but no decision was made. I could have made the boat bigger but I like a handy boat. I waited for my inner voice to speak.
On my door, way back in time, I had written
Cape Horn East to west. Lat 50 S to 50 S as an interesting alternative.
On the night between 30 and 31 December 2021 I woke and started thinking. There is a lot of depressions passing Cape Horn. I thought if I could make reefing more easy and take advantage of the shifting winds I may stand a chance of reaching the Pacific that way.
Then I came to think of the Ljungström rig.
Navigateur Yann Quenet was using it on his Baluchon.
It has a free-standing mast that can rotate. By turning the mast on the boom-less rig the sail area is reduced in the same way as a furling jib.
It is a Swedish invention from 1933 by Fredrik Ljungström. You can still see some of the old boats around here in Sweden.
It works, but there is some problems with it. The sail is triangular, therefore the mast must be tall to give sufficient sail area and there is no boom to facilitate downwind sailing. The sheeting point is too low.
I got around these points in the following ways.
To increase the sail area I used a vertical club as the Chesapeake Bay racing log canoes. The vertical clubs I can make of composite to minimize their turbulence and make them light.
To overcome the problem with the sheeting point I will rake the mast aft 20 -25 degrees or so. That way I can sheet my two mainsails like foresails.
The rake also moves the center of effort aft. I like that because my side by side masts are forward of the fore bulkhead to not be in my bed and I like to have more weather helm. Rake is good for offshore work, as it gives a lifting force and keeps the boom from dipping in the water and possibly breaking when the boat rolls deeply.
This rig creates less forces on the masts as the lugsail hangs on the top of the mast therefore I can make it longer and more tapered.
The Ljungström mast can be rotated to get the sail always on the lee side. This will make the suction side more smooth reduce turbulence.
The chances of my succeeding in doubling Cape Horn is uncertain as I will have strong prevailing winds and currents against me, but that makes the undertaking interesting. Even if I do not succeed all is not lost as I can do as Captain Bligh did.
He had for a month unsuccessfully tried round Cape Horn in Bounty but was finally defeated by the stormy weather and opposite winds and forced to head east repair damage in Cape Town and then take the longer way to the pacific by sailing east by way of Australia.
If the canoe yawl Exlex proves to be fast and able, only then will I try the Cape Horn alternative. My hope is that she be a good boat.
Below photos
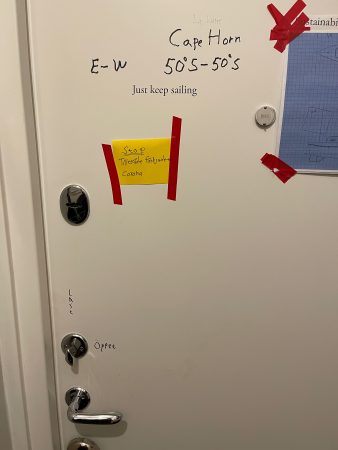
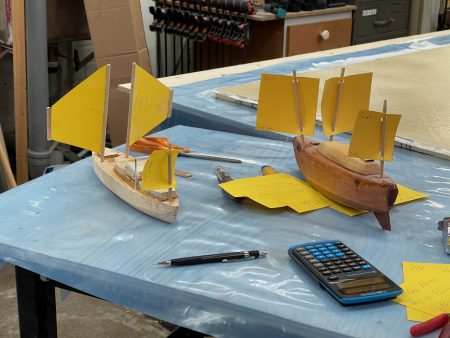
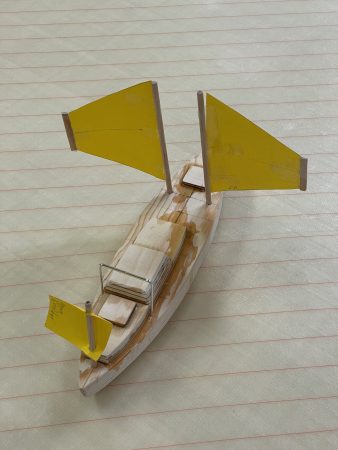
In conclusoin: I will try a new rig, more easy to reef, I will try Cape Horn. If I reach the Pacific via Cape Horn NZ will have to wait.
Plese support my project with donations.
To be continued…
Regards Yrvind.
YRWINDS CONSTANT WEIGHT DIET
YRVINDS CONSTANT WEIGHT DIET
The word diet comes from old French, from Latin diaeta, way of living, diet, from Greek diaita.
To keep in shape , to be able to climb through my hatches I have started dieting. I have created my own diet version, Yrvind constant weight diet. It is a powerful diet. Here it is in three simple steps.
Step one. Decide on a desirable weight.
Step two. When Friday comes stop eating until the desired weight is reached.
Step three. Repeat every Friday.
My last meal before the fast was Thursday 25 Nov, my first meal after the fast was Sun 5 Dec 2021
Below is a list of how my weight changed during the fast, weights to the left, difference from day before to the right.
PLease support my project on Paypal or Swish.
Regards Yrvind.
Sam Holmes have done 40 min video in my workshop on Exlex the canoe yawl
Hopefully it will make my ideas more clear.
Regards Yrvind