Most of the work on the aft deck abowe the saloon is now done. What is left is to fillet and tape the seams between the different panels to get strong connections.
Below two pictures.
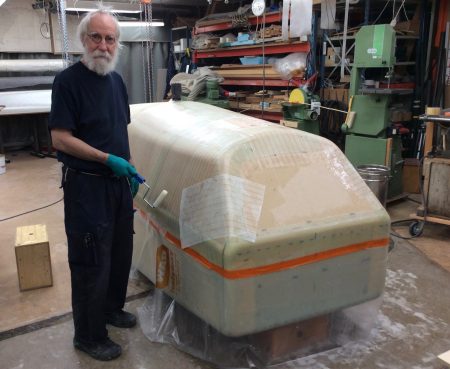
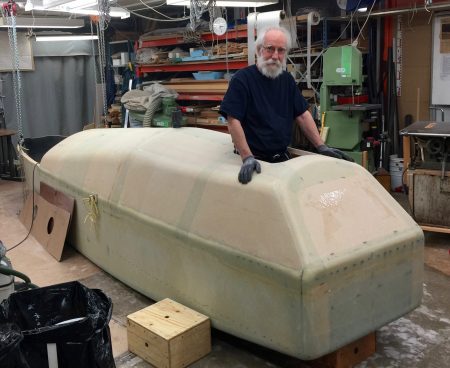
To be continued…
Regards Yrvind
Welcome to Yrvind´s website: small boat designer, builder, sailor & writer
Most of the work on the aft deck abowe the saloon is now done. What is left is to fillet and tape the seams between the different panels to get strong connections.
Below two pictures.
To be continued…
Regards Yrvind
Byrålådseffecten a english translation would be the drawer effect: This is what we engineers call the nuisance when a drawer gets stuck in a chest of drawers and it does not only happen to drawers; it happens to most sliding things that are wider than deep. It is a pain.
To avoid it I made an analyses and it turns out that the solution is surprisingly simple. Drawers that are wider than deep have little guidance and therefore not always move straight but turn. When they turn the short side of the drawer is not any longer parallel with the guiding sides. The drawer takes more space and gets stuck diagonally. The more you pull the worse the drawer gets stuck.
I said to myself: what geometrical figure does not get wider when it’s turned, obviously the circle, by definition. I use part of a circle segments have been cut away to make it almost like an rectangle. In this case when using it as a lid for the anchor locker I only lose 15 mm on the corners. Pictures will illuminate. A big lid would be to cumbersome so I devided into three peices.
Below some pictures.
This idea of preventing narrow sliding broadside to jam can be used on many applications. Companionways are mostly shaped narrover at the bottom that the washboard will not get stuck by the byrålådseffekten. Its a bit magical how easy the boards now slide thanks to the rounding of the corners.
I have now started on the deck of the saloon.
To be continued…
Regards Yrvind
The anchor stowage is now mostly done.
Below two pictures.
Next step is to do the lid and I got a good solution for that.
To be continued…
Regards Yrvind
A place for everything and everything in its place. It is important to get thing secured and easily accesible. That requaries a lot of detail and that takes time.
The arrangement for my bedroom is now nearly done. Today I finished lockers for my note pads. They are in A4 format and square lined 5 mm. Kollegieblock we call them and I really love them. I have used them since the 50-ies. They are exellent for drawing boats on using scale 1:40. One square then has a side of 20 cm, half a square is 10 cm.
Ipad and small computers also fit there. Two of these lockers are on each side. I use sliding lids. They work well I have used them on a few boats before 1968 the first time and on Exlex now 2018. The present ones are made of Tufnol a nice material I find.
Below some pictures.
To be continued…
Regards Yrvind.
Working on the ventilation ducts, the one for incoming air and the one for outgoing I had forgotten the interferences that always cases problems. Luckily in the last minute I noticed a note telling me not to forget the stearing ropes and a deck fitting. This was on the port side. Then silly enough doing the starbord side where there is no stearing rope I forgot that there is a deck fitting bolted to the inside. I have to cut up the starbord duct later to fit it. That cannot be done before the aft deck is in place. It would be more easy to do it now.
Below two pictures.
I will now cover the ducts done with glassfiber, turn the boat on even keel and continue elsewhere. Later I come back to the ducts. It will be more difficult to make them then becoause the aft deck will be on, but I do not build this boat because I like to have something easy to do. It will be a very good boat that will sail a wonderful voyage, so will be the next project as the previus ones have been. This life keeps me happy. Please donate that I can continue this wonderful life. If you enable me to do mistakes it will safe you from making them.
To be continued…
Regards Yrvind.
A boat should be dry inside even in heavy weather, and even after having been capsized and pitchpooled. At the same time it is a good thing to have a functioning ventilation system. Fresh air is a good thing.
1974 while attempting to round Cape Horn, I and the 20 feet boat I had built in my mothers basement the boat was capsized. A weak later in some of the strongest winds I have ever experienced she was pitchpooled. Water had entered through the ventilaters and created a mess. To avoid a repeat I figured out a system that would keep the boat dry. Two years later working with multihull designer Dick Newick on Marthas Vineyard I built my first system. It was provisional, just two hoses I put up when the waves started to break. On the boat I built 76 – 79 I made a permanent system, a aluminumtube from the deck to the bottom of the boat.
On Amfibie -Bris 85 – 89 I added a transverse duct so that intake an outlet was diametrically opposite.
On the yellow boat that I 2011 sailed to Martinique in I added a trap to the Doradebox thuse all the incoming air separated from water went into the cabin.
Now on Exlex Minor there is no deckhouse there is also stearing ropes that passes through the bulkhead with the two ducts of incoming and outgoing air and the door rotating around a horizontal axis is also there to add to the complexity in the region. This makes thinking necessary. However by slowly approaching the problem I now see a way. To simplify the problem, I have started with the given, a hole in the boulkhead and later I will do holes for the cowl vents in the deck. Then I will connect them with ducts that do not crossing each other.
Below some pictures.
There is plenty to do Christmas and New year will be spent working on the boat. If you have any money left please donate to my project. It is good for mankind with smal safe shallow draft ocean going boats propelled by sail and oar.
To be continued…
Regards Yrvind.
Tonight I have with the help of Stefan and Håkan laminated the outside of the deck.
I asked Stefan if he could give me a hand. I have 30 minutes he said after that I must go to a consert. Work took much longer after over an hour he had to leave. Lyckily Håkan turned up and stayed to the end, thuse rescuing me. It was filling the gaps I had cut to be abel to bend the top part of the deck that was the problem. The gaps used upp a lot more NM-epoxy thickend with silica than I had estimated. I had never done that before and sometimes new thing takes longer than planned. In the end thanks to my friends evrything went well. I am now ready to start designing and build the important ventilation system. Boats do capsize and pitchpoole. Whats happening in the Golden Globe race 2018 amply demonstrates that stormy weather do capsize boats that sails in high latitudes and causes a lot of damage. I belive that only a small boat well designed can come out of bad weather with no damage.
Below are some pictures.
To be continued…
Regards Yrvind
Today I have with the help of Håkan started the deck abouve my bedroom.
Here are some pictures.
To be continued…
Regards Yrvind
“There’s a Hole in My Bucket” is a children’s song, based on a dialogue between two characters, called Henry and Liza, about a leaky bucket. The song describes a deadlock situation: Henry has a leaky bucket, and Liza tells him to repair it. To fix the leaky bucket, he needs straw. To cut the straw, he needs an axe. To sharpen the axe, he needs to wet the sharpening stone. To wet the stone, he needs water. But to fetch water, he needs the bucket, which has a hole in it. Harry Belafonte made a famous record of it in 1960 well worth listening to.
After finishing the hull and I started to make the lunch boxes, but before installing them I had to do the ventilation system so I started in my bedroom with the stovage, but before finishing that I had to do the ventilation system but before doing that I had to do the deck, but before doing the deck I had to do the mastholder.
I have also started on the coamings for the two hatches.
Now the mastholder is done ready to be installed, the deck is laminated on the inside ready to be put on, in other words the deadlock is broken. Soon there will be some progress.
Below some pictures.
To be continued…
Regards Yrvind.
Today 18:30 we started to mix the NM-elastic epoxy. Helping me were Håkan Stefan Peter and Petter. All went very well although my original plan had to be changed for a better one suggested by Petter. One should always chose helpers that are smarter than oneself.
Below are some pictures taken by Håkan. The reason you cannot see him is that he is behind the camera.
I like also to thank Lagermetall in Örebro who supplied the bronze plate and Wevik Maskin AB here in Västervik who bent the palte to shape.
To be continued…
Regards Yrvind.