Not many people today sail without autopilot or windvane.
I do becouse its simple, cheap, takes up no space and is fun, also few things can go wrong.
A few things have to be kept in mind, no play in the system and a possibility to adjust the rudder angle rather precicesly.
On Bris I had a wheel and it was geared 10:1 to the rudder, that is ten turns of the wheel turned the rudder once. Adjustments of the spokes had to be done not more than a few millimeters at the time as the wind did change.
On Exlex there is no rudder. The stearing lines goes directly to the tillers. I realise i need a product to reduce line movement. The boat will move about in big waves. I have come up with the following device I call it a “Vector Winch”.
It works on the swig principle. The way you haul a line, especially a halyard, taut manually.
Theoretically it has a power range from infinity to minus 2.
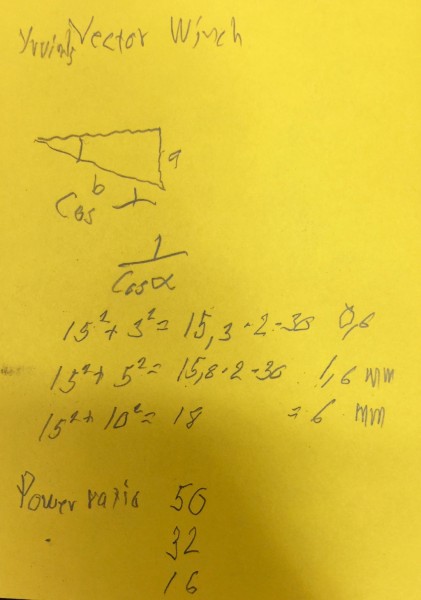
For 30 cm between the fairleeds if you mowe the line 30 mm at right angle to the tension the line will be 0.6 millimeter shorter a reduction of 50 to 1.
50 mm shorten 1.6 millimeter reduction 32 to 1.
100 mm shortens line by 6 mm.
This way I can fine adjust my rudders.
Photos below show a mock up. It works wery well.
There is 30 cm between the fairleeds and two line jammers.
Me happy with my device.
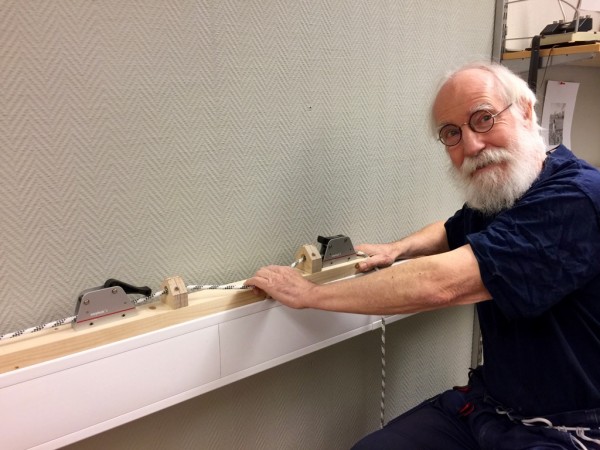
Tension the winch:
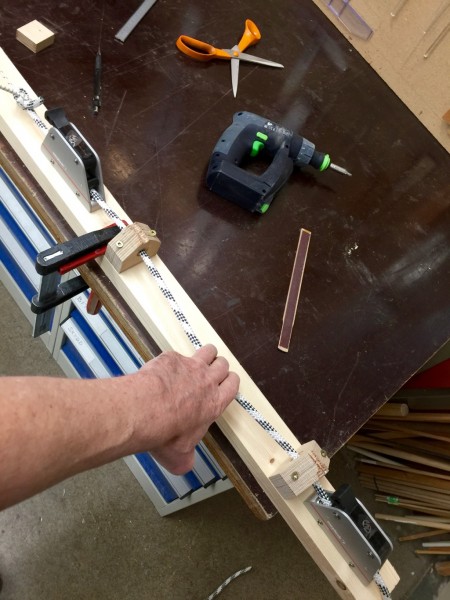
Below Photo from the side:

To use the device, release the jammer close to the tiller, tension rope the desired amount, close the jammer, release the secound jammer, take up the slack, close the secound jammer. Done.
These products will be mounted abouve my bunk where i spend most of my time reading sleaping drawing on the next boat “Boat Ideal”. When I am in other parts of the boat the jammers are released that way I can steer from every other part of the boat also.
To be continued…
Regards Yrvind.
Like this:
Like Loading...