Working on the ventilation ducts, the one for incoming air and the one for outgoing I had forgotten the interferences that always cases problems. Luckily in the last minute I noticed a note telling me not to forget the stearing ropes and a deck fitting. This was on the port side. Then silly enough doing the starbord side where there is no stearing rope I forgot that there is a deck fitting bolted to the inside. I have to cut up the starbord duct later to fit it. That cannot be done before the aft deck is in place. It would be more easy to do it now.
Below two pictures.
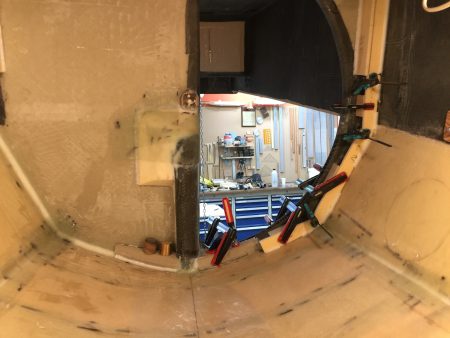
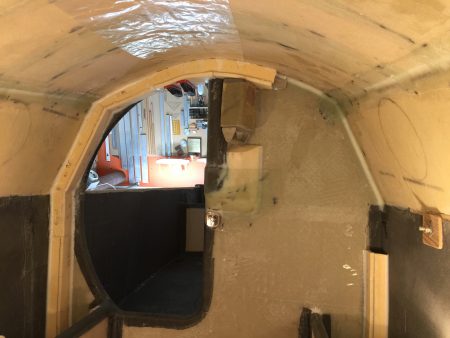
I will now cover the ducts done with glassfiber, turn the boat on even keel and continue elsewhere. Later I come back to the ducts. It will be more difficult to make them then becoause the aft deck will be on, but I do not build this boat because I like to have something easy to do. It will be a very good boat that will sail a wonderful voyage, so will be the next project as the previus ones have been. This life keeps me happy. Please donate that I can continue this wonderful life. If you enable me to do mistakes it will safe you from making them.
To be continued…
Regards Yrvind.