VISITING FRIENDS
As late as Sunday night 12th of August 2018 the idea was to first to build a prototype of plywood before starting on the real composite Exlex Minor. Somehow, for several reasons, very late in that night I changed my mind. The train of thoughts started with me having problems finding good marine plywood. Some people say that if encapsulate the plywood in epoxy you can use the cheapest plywood. Maybe so but the idea of using an inferior product goes against my grain. Then it was the spoon bow; with thicker Divinycell it would be easier to sculpture a nice round shape, an other reason was that the plywood version and the composite version always would be different due to different skin thicknesses 18, 12 and 9 millimeter for bottom side and deck for plywood versus 25, 40 and 20 for the Divinycell core. A third reason was I was eager to get sailing and would be more motivated if I was working on the real boat. It was a complex decision with several factors working for and against the final decision. During the night I kept tossing ideas against each other. Finally when I fell asleep Monday morning the decision was to go composite. I hope I made the right decision, time will tell.
When I woke up I phoned Anders Lindström at Diab in Laholm, the Divinycell people. Over the phone we worked out what suitable core materials where in stock.
Then I phoned Sten Fransson at Tanso in Jönköping for Carbon fibers peel ply and protecting gloves. He said I could come by. The carbon fiber will be used on the inside laminate to absorb impacts. More about that later.
Finally I phoned Gunnar Malmgren at NM-epoxy in Ytterby just outside Kungälv telling him that I was coming over to the west coast and asked if it was OK if I came by to pick up epoxy
Håkan Johansson at Mekonomen Västervik lent me a big van.
Tuesday 14 of august in the morning I started. My first stop was Tanso Jönköping. Sten took me to lunch and I explained my project and what I needed.
From Jönköping I drove from Ytterby near Kungälv where Gunnar greeted me,
then finally to Laholm. Now it was late. Being frugal I slept in the big car. My money would be better spent on the boat than on a hotel.
Early next morning Anders showed me around in the factory and helped to stove the Divinycell in the car.
On Wednesday afternoon I was back in Västervik. Håkan helped me to unload the car.
Today thuesday 16 of August I have again borrowed Håkans van now to porchase plywood and particle board for the moulds. The ones I made for the plywood version is of no use now as I will build differently. Now I can start to build in earnest.
Below Håkan and the van he lent me.
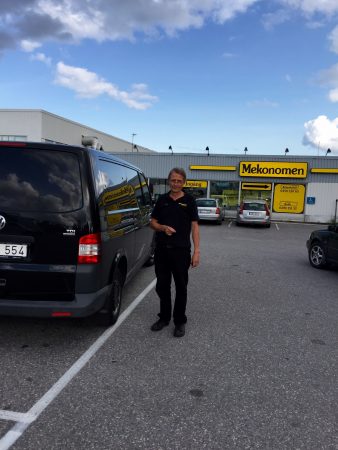
Below Sten at Tanso
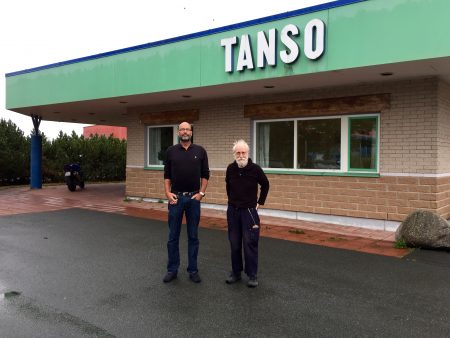
The picture below is from inside the factory, showing a friendly girl tempting me with apples and a machine that works graphite.
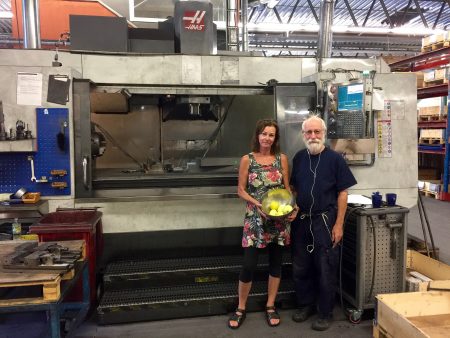
Below Gunnar showing me around in the epoxy factory here a mixing machine.
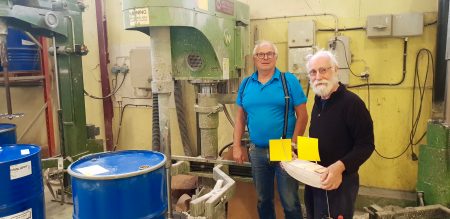
Below a filling up machine.
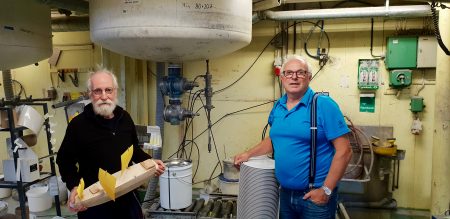
Below some of the MN-epoxy for the new boat.
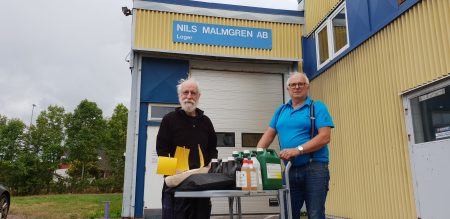
Below Anders showing me around in the Diab factory. The machine shown grinds the Divinycell sheets to exact thickness.
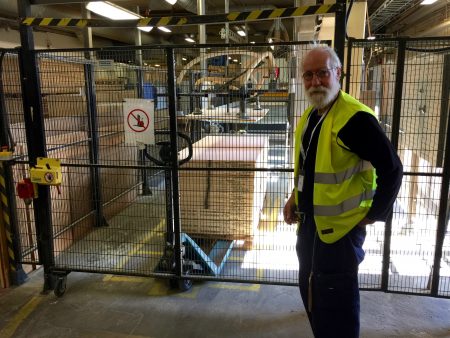
Below me and Anders and the Divinycell sheets in the van. My sleeping bag is in the blue sack between us.
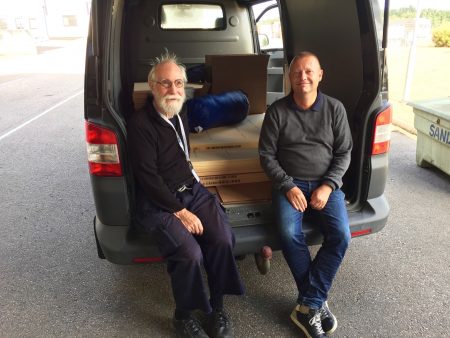
I am now safely back home in Västervik working on Exlex Minor. I am thanking everyone supporting me and Exlex through Swish and Pay Pal. Please continue. Your contributions are needed.
To be continued…
Regards Yrvind.
Like this:
Like Loading...